運搬車を改造して自作したコンパクトな高所作業車。ここではリンク3段に挑戦して失敗した様子や施した対策などについて書きます。
11.リンク3段の仮組立と試乗
最初はリンク3段で作業台(床面)までの地上高さ約2.7mとして組み立ててみました。
➀ 上昇開始時の跳ね上がり
リンクが複数連結されている構造では、最も縮んだ状態から伸ばそうとするときに非常に大きな力が必要になります。(理論計算2を参照)
この問題は実際には次のように現れます。
最初上昇開始時に油圧シリンダや最下部のアームにグッと負荷が掛かり、リンクが伸び始めるとその力が急に解放されて作業台が跳ね上がり、その後作業台が少しの間上下振動します。作業台が無い状態で自分が上に乗って上昇試験をしたときも同様な動きが起きました。
ここでリンク3段で仮組みして上昇させると、かなりひどい跳ね上がりと上下振動が現れました。人の場合は自分の足で調整して跳ね上がりを吸収してしまいますが、作業台はそんな調整はしませんので見事に現象が現れました。
なお、作業台の上昇速度が遅ければ、この現象も余り強くは表れなかったと思います。
➁ ねじれによる揺れ
最大まで上昇させて様子を見ました。元を少し揺らすと作業台が大きく揺れて非常に不安定です。特にリンク機構のねじれによる揺れが大きいことが分かりました。
➂ 最下段のアーム破断
作業台を最低に下げ、試しに自分も乗って上昇させはじめた瞬間に、「バキッ!」の音とともに床が大きく傾いてしまいました。原因を確認すると最下部のリンクアーム(単独)2本が中央部で見事に破断し折れていました。また、最下部の「日」の字型に溶接した方は、シリンダ接続点でアームが少し曲がっていました。
自分では大きな力が掛かるアーム端の強度に気を取られ、今回破断した部分については全く予想していませんでした。よく考えてみれば最下部のアームにはシリンダの推力が直接加わるため大きな曲げモーメントが掛かるはずです。また、上昇速度も破断に大きく関係すると思います。
これまで自分の体重だけで昇降テストをしているときは起きず、作業台の重さが加わった状態で破断しましたので、アームの破断限界がこのあたりにあるということにもなります。
私はいつも拙速で、失敗してその度に再認識させられていますが、今回も相変わらずでした。「失敗は成功のもと」改めて良い勉強になりました。怪我が無かったのも幸いです。
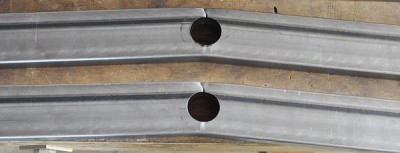
破断した最下部の単独アーム
➃ リンク数とシリンダ伸長速度
最初の理論計算の時にも上昇速度の心配がありましたが、実際の試乗でも速過ぎて少々危険を感じました。また、➀の跳ね上がりや➂の破断の原因にもなっています。
ここで、泣く泣くリンク数を2段とする決断をしました。地上高さは約2mとなりますが、作業台の上昇速度は2/3になり、最下段のアームに加わる負荷加重も2/3になると思われます。併せて油圧シリンダの伸長速度をもっと遅くすることを考えました。
⑤ 下降速度
下降速度は油圧ユニットのフローコントロールバルブで調整することができましたので、特に問題となることはありませんでした。また、油圧シリンダがクッション付きでしたので最下点に達するときには特に緩やかになってくれます。
12.アームを徹底的に補強
リンクを2段にしてもどのみち強度的には不足です。ネットで調べてみると一般的には安全率を考え、想定負荷の数倍の強度を持たせるのが一般的のようです。
「現在のアームを補強するか」または「もっと強度の大きい角パイプでアームを作り直すか」で悩んだ結果、現在のアームを補強することにしました。その理由は、ここまで時間と手間を掛けて作り込んできたことを再びやり直す元気が出なかったことと、補強作業により溶接のスキルを上げられると考えたためです。
補強の様子を写真に示します。ひどい溶接でこれで補強になるのかと言われそうです。
(この写真の物は全3段の内の使われなかったものです)
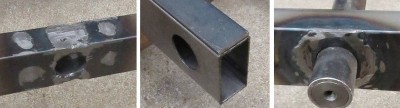
左:単独アーム中央軸穴 中:全アーム上面(準備) 右:日の字アーム貫通部外側
➀ 単独アーム中央の軸穴の補強
今回破断したアーム中央の軸穴はφ27.4の穴を開けただけの状態で、どう見ても強度不足でした。角パイプの中にぴったり入るサイズの角綱にφ27.4の穴を開けて中央まで差し込み、溶接して穴の周囲を補強しました。写真に示すように、角パイプには要所に穴を開けて中の角綱と溶接してあります。(写真のアームは破断した物で、破断部を切断して角棒を差し込み溶接してみました)
➁ 単独アーム端の軸穴の補強
単独アーム端もφ27.4の穴を開けただけの状態でした。こちらはSGP黒ガス管25Aをリング状に切断してはめ込み、管内径と穴を合わせて溶接(MAG溶接とTIG溶接)しました。管25Aの内径は27.6mmで軸穴とほぼぴったりです。
➂ アームの上面(破断側)の補強
アームの上面の引っ張り強度を高めるために、写真に示すように全てのアーム上面に平鋼をあてがい溶接(TIG溶接)しました。何と角パイプ全体が日本刀のように反り返るという新たな難問が発生し、自分が如何に溶接素人かを改めて自覚しました。角パイプにはある程度の高さがあるから大丈夫だろうと思ったのですが甘かったです。対策は、端から一気に溶接しないよう、全体にわたって点付けしてから少しずつ溶接するなどして、反り返りを減らすこと位でした。(事故で曲がっていたところは真っ直ぐになりました「笑」)
➃ 「日」の字型組アームの丸パイプ貫通部の補強
この部分の内側は既に溶接がされていますが外側は無処理でした。元々はめ込まれるt1.6の擦れ防止用ワッシャを溶接(TIG溶接)し、肉厚を稼ぎました(写真参照)。また、アームの内面から見える範囲は内面から溶接(MAG溶接)しました。
平鋼 t3×25 角鋼 22.5×46.5×100 SGP黒ガス管25A 外形φ34 × t3.2 内径=34-3.2×2=27.6
13.上昇速度を調整可能に
本当に困ったときは スタクセル・エンジニアリング様 に相談です。油圧シリンダの伸長速度を調整する方法についてご相談したところ、「速度調整弁」なるものがありお送り頂けるとのこと。早速頂いて油圧回路に挿入しました。弁に付いている調整ノブを回すことにより、油圧の速度を調整できるようになりました。なお、弁の挿入にあたっては複数のアダプタ(継ぎ手)が必要になりました。また、油圧の流路幅を調整して流量を調整するタイプですので「流量を遅くすること=ポンプの負荷を重くすること」になり、効率的には悪くなるようです。

速度調整弁の追加
速度調整弁 ポートR1/8 × 2 ノブとポート間の距離が長い方が一次側(ポンプ側) 異径アダプタ SR-13-3×6-SS Rc1/8-G1/4オスシート(清水製作所) 直角アダプタ UL-90-1613-6-SS G1/4メスシート-G1/4オスシート(清水製作所) 他
注 速度調整弁の挿入位置
スタクセル・エンジニアリング様のご助言では、ホース外れ事故時などの安全面から、油圧シリンダの押し側ポートにはできるだけ内径の細いニップルなどをかました方が良いとのことです。この速度調整弁もできれば油圧シリンダに直結するようにとのことでした。
実は油圧ポンプの最高圧力が12MPaであるのに対して油圧ホースの耐圧が7MPaで耐圧不足でした。かえって危険と判断しとりあえず調整弁を油圧ユニットに直結し、調整弁の二次側(シリンダとの間)にホースを接続しました。
現在はホースを 耐圧20.5MPaのものに変えています。
後になって検討し直していると、最初の素人判断がかなり危険を伴うものだったと改めて感じます。「それでも作ってみたい!」困ったものです。
関連ページ
高所作業車自作 概要
高所作業車自作 その1 主要材料調達
高所作業車自作 その2 理論計算1
高所作業車自作 その3 製作
高所作業車自作 その4 仮組立とアーム破断
高所作業車自作 その5 塗装と最終組立
高所作業車自作 その6 理論計算2
高所作業車自作 その7 強度計算にチャレンジ